制造业的发展,零件加工过程的质量追溯变得越来越重要。传统的质量管理往往依赖于人工记录和手工追溯,容易出现漏洞和错误。因此,为了提高零件加工过程的质量控制水平,我们需要开发一种高效可靠的质量追溯系统。
本质量追溯系统的设计方案主要包括以下几个方面。
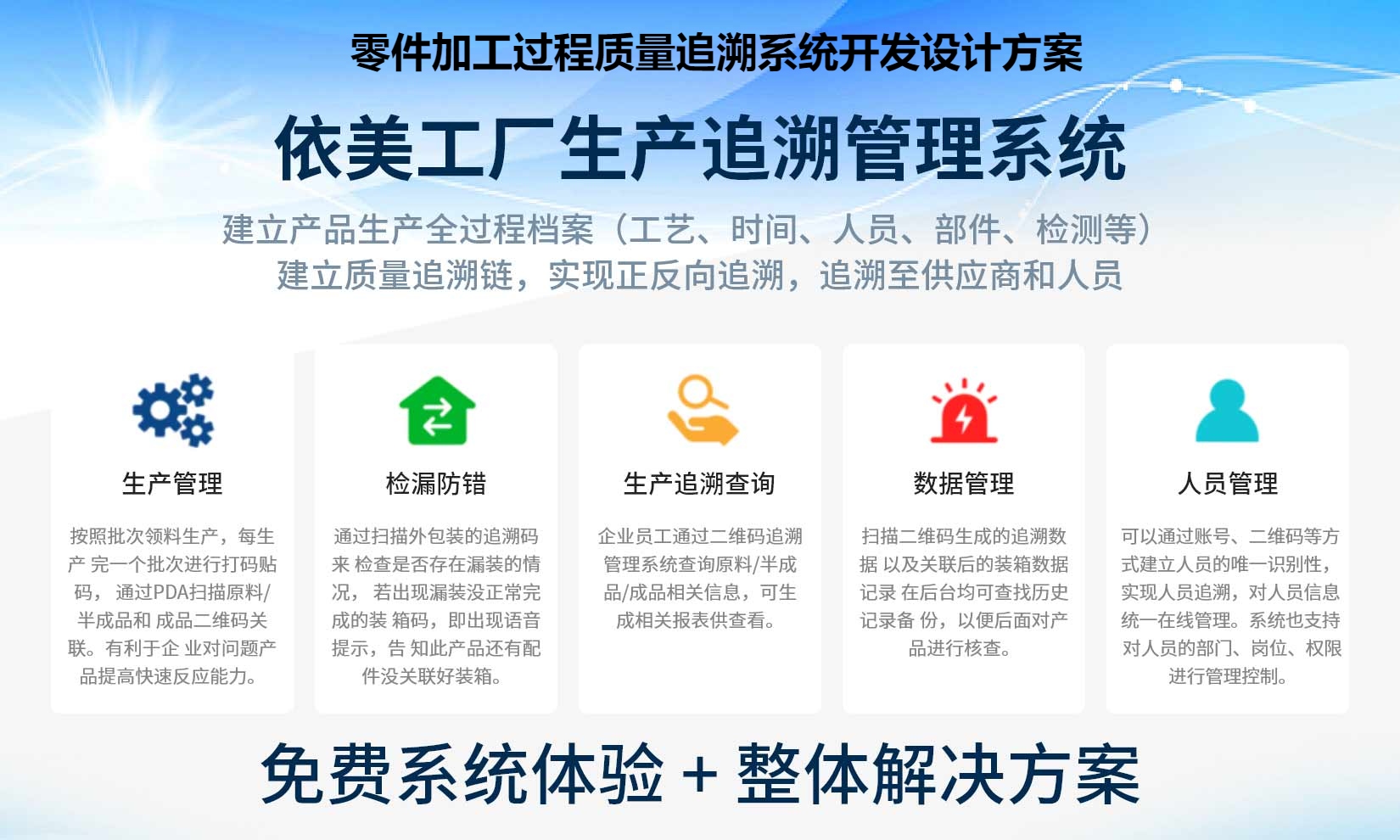
1. 零件标识和编码:在零件加工过程中,每个零件都应配备唯一的标识码。可以采用二维码、电子标签等方式进行标识,保证零件的唯一性。
2. 数据采集和存储:在零件加工过程中,需要采集和记录相关的质量数据。可以使用传感器、检测设备等来实时监测零件的加工参数和质量指标,并将数据存储到数据库中。
3. 追溯和查询功能:系统提供追溯和查询功能,可以通过零件标识码快速查询该零件的加工流程和历史数据。系统可以根据零件标识码,追溯零件的原料来源、加工流程、操作人员等信息,确保零件加工过程的全方位质量追溯。
4. 异常处理和预警功能:系统可以自动监测和识别异常情况,并提供预警功能。当零件加工过程中出现异常或超出设定的质量指标范围时,系统会及时发出预警信息,以便及时采取纠正措施,确保产品质量符合要求。
5. 数据分析和报表生成:系统可以对采集到的数据进行分析,并生成相应的报表。通过对数据的分析,可以评估和改进零件加工过程的质量控制水平,为提高零件加工质量提供科学依据。
通过上述设计方案的实施,可以实现零件加工过程的质量追溯和控制。该系统不仅可以提高零件加工过程的质量管理水平,减少人工记录和追溯所带来的漏洞和错误,还可以提高生产效率和减少成本。同时,该系统还具有良好的可扩展性和适应性,可以适应不同规模和类型的零件加工生产企业的需求。
零件加工过程质量追溯系统的开发设计方案将有助于提高零件加工的质量控制水平,提高生产效率和降低质量风险,对于企业实现可持续发展具有重要意义。